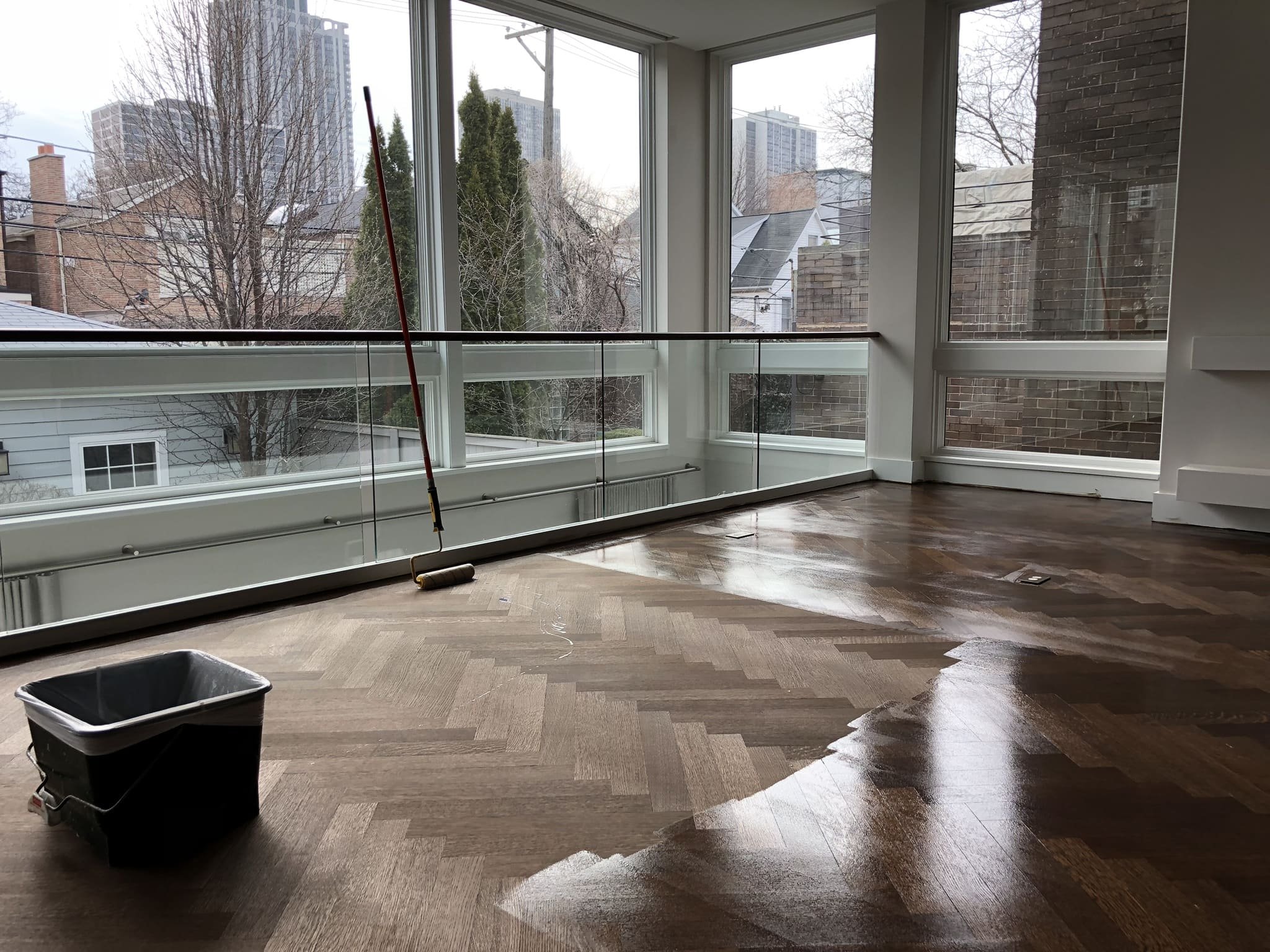
CHICAGO HARDWOOD FLOORING BLOG
Tips and tricks for all your hardwood flooring needs by a local flooring company in Chicago.
How Durable is Rubio Monocoat and is it the Best Choice?
Rubio Monocoat is a popular hardwood floor finish known for its durability, resistance to wear and tear, and easy maintenance. Learn more about this finish and its benefits as we explore all you need to know about Rubio Monocoat! If you need your floors done around the Chicagoland area, please reach out to us.
Hey guys, Patrick here. This week I decided to put together a blog post for a finish we use very regularly, Rubio Monocoat. We’ve applied a ton of this product over the years. I hope you enjoy it!
Wood captivates with its natural charm and elegance, but keeping it in top shape is a real task. That's where Rubio Monocoat comes in – a linseed-based hardwax oil that not only preserves the beauty of wood but also offers unmatched durability. It bonds deeply, protecting your wood from daily wear while highlighting its natural grain. Let's learn more about what makes Rubio Monocoat so resilient and so special. If by the end of this you still feel like learning more about Rubio, please check out this other extensive post I’ve made about it.
Exploring The Resilience Of Rubio Monocoat
One liter can of Rubio Monocoat 2c Oil. This is the main Rubio Monocoat product used for floors
Rubio Monocoat stands out as a superior choice for protecting wood. This wonder oil is not just another wood finish – it is a protective shield that molecularly bonds with the wood, providing robust protection that lasts. The result? A natural look of the wood that’s preserved and protected, no matter what wood species you’re working with. The fact that the finish bonds from the inside, and doesn’t build protective film layers from the top side, allows for a very ultra matte appearance.
Rubio Monocoat is lauded for its:
Stunning aesthetics
Durability
Easy Re-Oiling Process
Vast Color Selection
Rubio works great for all natural wood surfaces. Today, I’ll go over its resilience in detail, from the scientific basis of its durability to its performance in real-life conditions. I’ll also go over my personal experiences with this product.
The Science Behind Rubio Monocoat's Durability
At the heart of Rubio Monocoat’s remarkable durability lies its unique molecular bonding process. Unlike traditional oil finishes that simply sit on top of the wood, Rubio Monocoat permeates the wood fibers and bonds with them at a molecular level. This creates a durable, long-lasting finish that:
Protects the wood from the inside out
Enhances the natural beauty of the wood
Requires only one coat
Does not contain any harmful chemicals or VOCs
With Rubio Monocoat, you can trust that your wood surfaces will be protected and look stunning for years to come.
The choice of finish, including the color, also plays a role in the durability of Rubio Monocoat. For instance, the Pure finish is not pigmented but has the natural hue from the linseed oil, providing a pure finish, while the Natural finish is pigmented with yellow/white tones to balance the richer shades generated by the linseed oil.
Regardless of your color preference, Rubio Monocoat boasts an extended shelf life and a quick curing time, promising a finish that endures as long as your passion for wood. HOWEVER, you should note that only the 2c oil product can be used for actual hardwood floors. The added “B part” hardener is 100% required if you are going to put this product on your floors.
Real-Life Durability Tests
Pouring some Rubio out onto a brand new Rift & Quartersawn White Oak floor
Rigorous lab tests are great, but what about real-life conditions? How does Rubio Monocoat hold up against the daily grind, the accidental spills, and the household pets?
Besides being water-resistant, Rubio Monocoat also stands up admirably under high foot traffic when properly maintained. We’ve applied this many times over the years, and any homes we revisited that had Rubio Monocoat applied all held up very well, apart from a couple of instances. I’ll go further into detail on my personal thoughts about the durability of this product below.
Please note, that even though this product is considered durable, you’ll still have to apply a regular maintenance re-oiling coat probably every 3-6 years to achieve the most optimal results and performance. You will also have a couple of other factors to keep in mind, too, like the fact that you can only use their Rubio Soap cleaner to wash your floors. Don’t worry, I’ll go into this in more detail down below.
Longevity: Shelf Life And Cure Time
A major factor in the durability of a wood finish is its shelf life and cure time. Rubio Monocoat does well in both these aspects. Being a natural oil, this product has a prolonged shelf life, even when it isn’t used. However, once it is mixed with the hardener, you only have an open working time of a couple hours.
When it comes to cure time, Rubio Monocoat Oil Plus 2C is 80% cured in two days and fully cured within five days. This fast curing time means your wood surfaces will be ready for use in no time. And once cured, Rubio Monocoat provides a lifetime of protection. The first maintenance should be conducted between 3-6 years, ensuring a long-lasting, beautiful floor for many years to come.
Protective Qualities Of Rubio Monocoat Oil
Applying Rubio Monocoat using the troweling process
Protection is the cornerstone of any good wood finish, and Rubio Monocoat is no exception. It offers top-notch protection from heat, water, and wear, thereby increasing the durability and longevity of wood.
Whether you’re looking to protect a curly maple table or a white oak floor, Rubio Monocoat 2c Oil is up to the task. With its wide range of colors, you can find the perfect hue to enhance the natural grain of your wood and achieve the exact look you want. An added bonus? Rubio Monocoat Oil Plus 2C colors can be mixed and matched for a genuinely customized finish. What you’ll find is that this product is also incredibly popular with furniture makers as well as cabinet and table builders. To be honest with you, the product works very easily in smaller applications such as that. For an entire flooring project, this can still be quite a tricky product to tackle. But that’s why I’m here to help!
Water Resistance
In the battle against water, I’d say this product does fairly well. But, I’m going to be honest with you here and realistic. No, it isn’t going to make your floors waterproof, nothing will. However, it’s also important to note that, even though this will offer protection against water spills, it might not offer the best protection for such mishaps.
Why do I say this? Because I genuinely believe that Rubio Monocoat has a much better scratch resistance than water resistance. This means that the product will probably hold up better to scratches then it will to spills. That doesn’t mean it isn’t going to protect your floors from a spilled glass of water, but what is does mean is that you should definitely still wipe up a water spill, if it does happen.
Defense Against Daily Wear
This category is where I really feel like Rubio actually stands out quite a bit. I genuinely believe that Rubio actually has a much better scratch resistance than most other flooring products on the market. This includes both oil & water based finishes. I think for scratch resistance, Rubio beats these by a mile.
The issue? The issue is again, the water resistance. The wood not having a top layer of film protection means that anything that does get spilled onto the floor will permeate through the protective layer quicker and could cause actual staining or damage to the floors. For a small water spill this usually isn’t a big deal. But what if your pets throw up on the floor? And what if you don’t see it right away? Yep, as you can imagine, THAT is the main drawback of the product. That chemical resistance certainly suffers especially when something acidic sits on the floors for too long.
Maintaining The Strength Of Your Rubio Wood Floor Finish
Jon applying Rubio Monocoat to the stair posts by hand
Having a beautiful Rubio Monocoat floor & finish is one thing; maintaining it is another. But don’t worry, Rubio Monocoat is designed to be super low-maintenance, so you can enjoy your beautiful wood surfaces without any hassle!
…but is it actually? You decide.
Cleaning And Care With Rubio Monocoat Soap
Cleaning a Rubio Monocoat finish is a breeze, thanks to Rubio Monocoat Soap. But there lies the problem itself…because you can’t clean the floors with anything besides their very specific soap.
But Rubio Monocoat Soap does more than just clean. At least, that’s what they claim. The reasoning behind having to only use their specific cleaning soap, is that it helps to restore the surface back to a freshly oiled condition. That means every time you clean your floors, the soap acts as a very light re-oiling to your floors. This helps in better concealing minor scratches and preserving the look of the finish.
So is any of that actually true? Well, yes, to a certain extent I’d say it’s true. You certainly have to use their soap to wash your floors, there is no denying that. I definitely agree that the soap, being a natural oil too, has great properties that help preserve the floors. But I think, the bigger thing to keep in mind, is not the benefits that cleaning your floors with this soap will have. No, the more important thing to remember is that if you don’t clean the floors with this product, you’ll likely ruin them. If you use a harsher cleaning agent on floors finished with Rubio Monocoat, you will entirely ruin the surface sheen. You will make the product uneven not only in color, but in appearance.
Refreshing Your Rubio Monocoat Finish
Buffing Rubio Monocoat deep into the grain of the White Oak flooring (don’t mind my McDonalds bag on the window lol)
Alright, so maybe cleaning floors with Rubio Monocoat isn’t super duper easy after all. But that’s fine, because having us come in to maintain them is super inexpensive and easy, right!?
Well, again, to a certain extent. Yes, it’s very easy to have us come back, and reapply a new coat of Rubio to your floors. This WILL make them look almost like brand new again. It helps with a ton of surface scratches, and usually removes 96% of any blemishes or wear & tear.
So what’s the problem? The problem is you’ll have to get all of your furniture back out if you want us to come apply a new coat of finish. Sure, you can leave any bigger dressers and tables in place, we can certainly go around them. But, if you ever move out or put the home up for sale, the spots that did not recieve a new coat of Rubio will be dull. Can it be fixed? Yes, you’ll just have to do another re-oiling again.
Comparison With Other Finishes
So, how does this product stack up again other finishes like traditional oil and water based finish? Well, I think it’s tough to compare. Mainly because, the finish is so different compared to the standard ones offered. Here are some of the main differences. If you really want to do some more in depth research on how Rubio stacks up versus a normal finish, I’ve already got a post going way further into depth right here.
Hardwax Vs. Oil Polyurethane
When compared to other finishes, the hardwax oil wood finish, Rubio Monocoat, stands out in several ways:
Hardwax finishes are applied by hand and provide a more natural, matte appearance.
Oil polyurethane finishes offer a glossy finish but may need to be sanded and refinished over time. They also smell atrociously.
Rubio Monocoat offers a very wide range of color options. Many of these color options are not available with traditional staining products.
Personal Experiences With Rubio Monocoat
Final buffing pass, removing any excess Rubio from the floor. This is by far the most important step
Hearing about the benefits of Rubio Monocoat is one thing, but seeing it in action is another. Nothing beats personal experiences when it comes to understanding the true value of a product. And believe me, I’ve got plenty of experiences to share.
From Floors To Furniture Pieces
Applying Rubio Monocoat Pure to a built-in kitchen cutting board
Throughout the years, I’ve used this product so much. I’ve applied it to almost every species of wood you can think of, and I’ve applied it to more floors then I can count. But that isn’t it. I’ve also applied this product to cutting boards, chairs, tables, shelves, bookcases, and all sorts of furniture.
Finished picture of the same cutting board half an hour later
So what are my honest unfiltered thoughts? It’s an amazing product. But it’s only amazing if you specifically know what you want, and if you understand all of the care and maintenance involved with this product. I like to use a car analogy, so car guys stick with me here. This product is like buying a brand new Porsche GT3 RS. But after you buy that Porsche, what do you do? You don’t take it through the auto carwash, do you? No, you’ve got to get this thing hand washed. And after you get it hand washed, you need a ceramic coat applied to the surface. That ceramic coat needs to be maintained and reapplied once it starts getting worn down…well this works the exact same way and it is the exact same concept.
All in all, I think this is a very cool product. But it works well only for homeowners without a budget, where appearance and color satisfaction are much more important than actual project budget or maintenance worries. I believe situations where the client or designer want the floors to look like super matte, like raw wood, are ideal for this product. Also, situations where designers want crazy specific or difficult to achieve colors also play very well into this products strong side.
Summary
And there you have it, folks – my quick take on the wonders of Rubio Monocoat. I aimed for a crisp, clear rundown rather than a lengthy discourse. For those of you craving a deeper dive into how Rubio Monocoat stacks up against traditional finishes, I've got just the thing – check out my detailed blog post here. And remember, I'm always here for your questions and thoughts. Don't hesitate to drop them in the comments below. Until our next flooring adventure, stay fabulous, dear readers!
Rubio Monocoat vs Standard Floor Finish: What are the Differences?
Rubio Monocoat and standard oil\water based finishes are both very popular options for hardwood flooring, but they have different properties and characteristics. Learn about the differences and benefits of Rubio Monocoat vs a standard finish in our newly updated post.
Hello everyone, Patrick here! I'm excited to bring you a special update today. I've been revisiting and refreshing all my old Rubio Monocoat blog posts, starting with the most popular one. This post had some information that needed a bit of updating, so here's the newly revamped version for 2024! As we embrace the holiday season and look forward to the new year, I wish you all joy and happiness. Now let’s dive into this updated blog post together and discover the latest insights on these wood floor finishes!
Picture this: a beautifully crafted wooden floor under your feet, its texture smooth and inviting. Now, think about the vital layer that sits atop it - the finish that defends the wood from the hustle and bustle of everyday life. This protective coating is more than just a shield against scratches and spills; it's an element of artistry that elevates the look and feel of your space. In today's post, we'll delve into a comparison between two renowned wood finishes – Rubio Monocoat and the standard oil/water-based finish. Join me in exploring these two options to determine the best choice for your hardwood flooring needs.
Freshly finished White Oak floors, rift and quartersawn. Finished with Rubio Monocoat Fume + Colored 2c oil
Key Takeaways
Rubio Monocoat & Standard Floor Finishes provide different levels of protection, durability, aesthetic appeal, and environmental impact.
The application process for each type of finish varies significantly, with Rubio Monocoat being tougher to apply but visually more appealing.
When selecting a wood floor finish, consider your needs and preferences as well as the scope of the project before making a decision on which is best suited for you.
Understanding Rubio Monocoat & Standard Flooring Finishes
Rubio Monocoat Hardwax Oil and standard oil-based/water-based finishes are at opposite ends of the spectrum when it comes to wood finishes. Whether it be for floors or for furniture, both tackle the same issue, protecting your wood. Rubio Monocoat, a single-coat, eco-friendly wood finish, enhances the wood’s natural beauty while offering long-lasting protection.
Standard wood floor finishes, on the other hand, require multiple coats of application. The application process itself, however, is much easier and quicker. These finishes are often favored for their hard, protective surface as well as cheaper cost & quicker application time.
What Is Rubio Monocoat?
Rubio Monocoat’s unique blend of natural oils and waxes offers the following benefits:
Molecularly bonds with the wood fibers, yielding a durable finish
Eco-friendly
Penetrates the wood, protecting it from within and not from the top
Highlights the wood’s unique features with endless variety of color options
The single-coat application process, a distinct feature of Rubio Monocoat, saves time and yields a natural, smooth texture and matte sheen that appeals to both sight and touch. Many rave about the single coat application step, and it is what initially convinced me to start applying this product back in 2016. However, this single coat application process is not just all rainbows and butterflies. It requires a TON of more manual labor to actually apply that singular coat. The way it looks afterwards though, absolutely stunning.
What Is A Standard Hardwood Floor Finish?
A traditional staple in wood finishing, standard oil-based and water-based finishes, are known for their hard, protective surface and high durability. These finishes permeate the wood fibers, fortifying them and furnishing a resilient protective coating. The main differences between these finishes versus Rubio, is simply the look.
Application process is also different for these finishes. Both water & oil based finishes are applied using a roller. There is a variety of other techniques that can be used, like troweling or t-baring the finish, but rolling is by far the most popular method. The finish layers are built on top of the wood floors, creating a strong protective barrier that will help against scratches and spills.
Comparing Application Process
While the end goal of both Rubio Monocoat and standard finishes is to protect and enhance the wood, their application processes differ significantly. This can be a deciding factor when choosing between the two, as the amount of time, effort, and tools required can greatly affect the overall project.
Application Of Rubio Monocoat
Michael applying Rubio Monocoat with a trowel
Rubio Monocoat application involves the following steps & a buffer IS required:
Surface preparation
Monocoat application
Fifteen-minute penetration
Excess removal
Seven-day curing period
For the application process, the Rubio must first be troweled into the wood by hand the entire time. Next, the finish must be allowed some time to sit, and penetrate into the wood. After, you can begin the removal process. This involves going over all of the flooring in a series a 3 steps after the initial application. Once with a red pad to buff more of the Rubio into the wood grain and knock down any raised grain. A second time with a white pad, to remove most of the excess Rubio on the floors. And then a third final time, going over the entire floors with towels and rags under your buffer to COMPLETELY remove any excess Rubio on the floors. -sidenote- I specifically linked the buffer pads so that you could see how much they cost. $30 for five buffer pads is not a mistake. You will need about 5 red pads and 5 white pads PER ROOM.
Keep in mind that all of this is happening while you are hustling your butt off to get through these 3 steps before the hardener inside of the Rubio begins to set. Once that happens, if you haven’t gotten through these steps, go ahead and just start pulling your sanding machines back out because salvaging the floors at that point is already too late. If you take too long and allow the Rubio to set too hard before removing it, this will cause the product to start gumming up and it becomes impossible to remove from the floors. And for those asking, yes, all of the edges must be completed at the same time by hand wherever the buffer does not reach. If you are doing stairs, they need to be entirely done by hand, too. For stairs and edges, I like to use these applicators. A single coat process sounds fun and like way less work, but really, in my eyes it’s just great marketing and nothing more. There is not a single thing about this finish that is easier to apply than regular finishes, unless of course all that you are going to be doing is just applying it to a tiny surface, like a table top or bookshelf.
Application Of Standard Finishes
The final coat of Loba Water-Based Finish being applied to a new floor
The application of standard finishes is much quicker and less laborious. It includes applying a couple coats of finish, lightly sanding between each whether it be by hand or with a buffer, and providing ample drying time. This process can also be labor-intensive and time-consuming, but for larger areas, it is much easier and quicker than Rubio. You can also do this by yourself, whereas with the Rubio you will at minimum need a team of 2 people to cover 1,000 square feet.
Please remember that the type of roller cover you use to actually apply your finish makes a huge difference. If you are specifically applying a water-based finish, these MUST be applied using a microfiber roller.
Aesthetic Differences
When it comes to the appearance of your wood surface, Rubio Monocoat and standard finishes offer distinct and beautiful results. The choice between the two depends on your aesthetic preferences and the look you aim to achieve.
Rubio Monocoat Appearance
Close-up of a floor in Highland Park, IL finished with Rubio Monocoat
Rubio Monocoat is celebrated for its capacity to amplify the wood’s inherent attractiveness. It’s most unique and distinct feature is the fact that it doesn’t build up a film layer on top of your floors. This means the floors will come out looking as matte as they possibly can, with very little to no sheen once fully cured. Rubio Monocoat is available in a variety of colors, all unique to Rubio, allowing for customization to suit your specific design preferences.
The outcome is a natural wood look no matter what color you choose, with a matte finish that elegantly highlights the inherent beauty of any wood that you apply it to.
Standard Finish Appearance
Brand new floors finished with Loba water-based finish. As you can see, even though they are a satin sheen, the shine level is quite different to Rubio as well as the overall appearance of the floors.
Conversely, standard finishes can modify the wood’s look, often intensifying its color and accentuating the grain differently. These finishes offer a range of sheens, from glossy to matte, which can dramatically affect the overall look of the wood. Over time, certain standard finishes can also cause the wood to darken or develop a yellowish sheen, which can add a vintage or aged look to the wood. It’s important to note, that the same will happen with Rubio Monocoat. Because it is a natural oil, it will still have the same yellowing properties over time as oil based finishes do.
Durability And Maintenance
Rubio Monocoat and standard finishes present their own unique advantages and disadvantages in terms of durability and maintenance. It’s important to consider how much maintenance you’re willing and able to do, and what kind of wear and tear the surface will be exposed to.
Rubio Monocoat Durability
Newly installed Rift & Quartersawn White Oak flooring in Downtown Chicago, IL finished with Rubio Monocoat Fume + Pure 2c oil
Rubio Monocoat is known for its excellent durability and resistance to wear and tear. Offering long-lasting protection, Rubio Monocoat can withstand heavy foot traffic and scratches. However, because it has no film layer on top, I’ve found that this finish suffers a bit more when it comes to chemical resistance & spills. The scratch protection is better than a standard finish, but the chemical and spill resistance certainly suffers.
With proper care, a wood floor finished with Rubio Monocoat can last a very long time. But, that care is much more in-depth than what most people think. For hardwood floors finished with Rubio, you must use their specific Rubio soap to clean the flooring. You can never use anything else, because their soap acts as a light re-oiling every time you clean the floor surface. It is also highly recommended to apply a fresh coat of Rubio Monocoat every 3-6 years to keep the floors looking as fresh as possible.
Standard Finish Durability
Close up of a fully finished floor with standard finish. As you can see, there is a clear film layer over the top of this wood, which creates a smooth surface that protects it from the top
Standard finishes offer strong protection for wood surfaces as well. Known for their hard surface and high durability, they form a sturdy bond with the flooring material, making them resistant to wear and tear.
Usually, the comparison I point out to clients between these two finishes that I’ve personally noticed over the years is this. I believe standard film forming finishes have better resistance to chemicals and spills. But, Rubio Monocoat is much more durable when it comes to scratch resistance. What does this mean for your home specifically? It means that if you have dogs or pets in general, probably opt for a standard finish. Sure, the Rubio Monocoat might hold up better to scratches from your dogs nails, but if your dog throws up on the floor, the standard finish will hold up whereas the Rubio will likely haze around that area if it is left too long.
Environmental Impact; Eco Friendly? Or Not?
Very old hardwood floors from 1980 finished using Rubio Monocoat Black 2c Oil
So I’m sure by now you’ve heard everyone talking about how eco friendly Rubio monocoat is. How it’s all zero VOC and incredibly safe to inhale or be around. Is it true? Years of a lot of clever marketing, I’d say.
Rubio Monocoat's Eco-Friendly Features
Rubio Monocoat’s prominent feature is its eco-friendliness. As a plant-based product, it uses natural ingredients and contains no volatile organic compounds (VOCs), which are harmful to both the environment and human health. Its rich formulation ensures a sustainable and effective solution for wood protection…or so they claim
Patrick, stop beating around the bush, is it zero VOC or not? Well, in my professional opinion, no, it isn’t. Now don’t get me wrong, if you use JUST the Rubio Monocoat 2c oil without the added hardener, then yes, it can be zero VOC. But if you are actually applying this product to floors or furniture, you need to add the 2c hardener, it isn’t optional. And guess what? That hardener is anything but zero voc. Yeah, I’m not kidding. Get a couple of rags soaked in this stuff, put them in a trash bag, and put it out on your lawn in the sunlight. I can guarantee you the garbage bag with rags from this product lights up ten times quicker then a bag filled with actual oil based stain rags. I have actually had rags from Rubio Monocoat start to smoke up almost in real-time in front of me after using the rags just ten minutes prior.
I want to conclude this section by saying that, even though it has VOC’s, I do prefer the actual smell of this product verses oil based and water based finishes. This product has a much more pleasant and natural smell, even though still unhealthy.
Standard Finish Environmental Impact
Standard finishes whether oil or water based typically contain VOCs, which are harmful to the environment and can contribute to air pollution. Additionally, the production and disposal of these finishes can also have negative effects on the environment, such as air and water pollution. Obviously, these are super minimal negative effects, but they are still negative. It’s important not to breathe this stuff in while it dries, and it’s important to be out of the home for any product that you apply to your floors.
Cost Comparison
I’m not going to spend too much time on this section. Mainly because, I think you can already assume which one is more expensive, haha. It is of course the Rubio Monocoat. The cost doesn’t even compare to be honest. Rubio Monocoat is definitely more so meant for the high-end, designer market. A liter of this stuff will set you back over $200 dollars. Keep in mind, most of the pricing you see online is for quarts and not liters. One liter of Rubio Monocoat will probably get you around 200 square feet or so.
Choosing The Right Finish For Your Project
Having covered the basics, you might be pondering, “Which finish suits my project best?” The answer to this question largely depends on your specific needs, preferences, and the type of wood you’re working with.
When To Choose Rubio Monocoat
Opt for Rubio Monocoat for a very unique, durable, and trendy option that accentuates the wood’s natural beauty. It’s particularly suitable for high-traffic areas or if you desire a more natural, matte finish. The main drawbacks being the cost and durability to chemicals as well as spills.
When To Choose Standard Finish
Select a standard finish for a more traditional look, or if you simply want something that will be fairly priced as well as easy to achieve. For Rubio Monocoat, you will need special craftsmen that know how to apply it. For a standard finish, any flooring company will be able to handle it. Standard finishes can offer a high level of protection and are ideal for projects where you want to customize the shine level of the finish.
Summary
In conclusion, both Rubio Monocoat and standard finishes offer unique benefits and have distinct features that can greatly affect the look, feel, and durability of your wood surfaces. Your choice between the two will depend on a variety of factors, including your aesthetic preferences, environmental considerations, maintenance needs, and budget. By understanding the properties and benefits of both Rubio Monocoat and standard finishes, you can make an informed decision that best suits your project needs. As always, if you have any questions feel free to reach out.
Frequently Asked Questions
What Are The Downsides Of Rubio Monocoat?
Rubio Monocoat finishes offer strong resistance to scratches, but they suffer in resistance to chemicals as well as spills. This is a downside of this product.
Is Rubio Monocoat Better Than Polyurethane?
Ultimately, it depends on your goals when choosing which flooring finish is best for you.
What Are The Advantages Of Rubio Monocoat?
Rubio Monocoat provides a durable protection for all types of hardwood floors. It only takes 1 day to apply, making it an ideal choice for flooring.
What Is The Difference Between Rubio Pure And Natural?
Rubio Monocoat Pure contains no pigment, whereas Natural has a creamy whitish/yellowish pigment, making the difference between them quite clear. Natural will give you more of a traditional amber color, whereas natural will give you a lighter and brighter color.
What Is The Primary Difference Between Rubio Monocoat And Standard Finishes?
The primary difference between Rubio Monocoat and standard finishes is that the former is a single-coat, eco-friendly wood finish while the latter requires multiple coats and may have a higher environmental impact. The application processes for the two are entirely different.
The Pros and Cons of Stained Floors
Staining hardwood floors can give them a unique and beautiful look, but it also has its own set of pros and cons. Learn about the advantages and disadvantages of staining hardwood floors and how to decide if it's the right choice for you.
Installing hardwood floors in your home can be a great decision, but whether you install them yourself or buy a home that already has hardwood floors, that’s just the tip of the iceberg.
There is an awful lot that goes into preparing, treating, and finishing floors and every choice you make along the way can seriously affect the finished product. Nowhere is that truer than when it comes to staining.
While staining your hardwood can add warmth and depth to the floor and enhance the overall look of the room, if the process is not handled properly it can also have major unwanted results.
Before you proceed with staining, then, it’s crucial that you understand the pros and cons involved with this vital step.
What Exactly Is Staining?
This may seem like a very obvious notion, but you’d be surprised how many people actually confuse staining with finishing, and that can be a vital mistake as they are two very different processes. While finish is designed as a final, clear coat that simply adds a protective covering to your hardwood, stain actually colors the floor, enhancing or sometimes entirely changing the color of the wood.
Think of it as similar to painting a wall, with one crucial difference…if you wind up choosing the wrong color of paint it can be easily corrected. If something goes wrong with staining, however, you’ll have to re-sand the entire floor and start over again, which can be a time-consuming and frustrating process.
Once you understand the difference, you’ll need to be very careful about choosing your stain. There are a wide variety of colors to choose from and the one you select will depend on a number of factors, including the type of wood, the amount of light in the room, and the overall design.
Pros of Staining a Wood Floor
Though a lot can go wrong if the staining process isn’t handled properly, when it is done right there are plenty of ways that it can enhance a room. Color, warmth, shine and depth can all be enhanced with the right choice of stain and the correct application. Done correctly, your finished room can have the stunning, natural look that you see in home décor magazines.
Some specific benefits of staining can include the following:
Achieving the elegance of dark wood – most natural wood is light in color, but with a rich, deep stain applied, you can get the drama of dark wood. This is a look that is very popular in magazines today and one that can be a major selling point in the real estate market.
Copying the look of a certain wood type – even if you can’t afford more expensive types of wood or if you buy a home with one type of wood but want the look of another, staining can give you that option. Staining a lighter wood with a rich cherry can help give it the depth and dimension of natural cherry.
Some lighter woods, like oak, aren’t very flexible making it difficult to achieve elaborate designs like a herringbone or lattice, but with stain, you can use a more flexible wood to get the pattern you like and then achieve the look of oak with the choice of stain.
·Accentuating the natural beauty of wood – perhaps the biggest advantage of staining is its ability to bring out the natural patina and accentuate the grain, giving a warmer, cozier feel to your room through the richness of wood flooring.
Cons of Staining a Wood Floor
Of course, as with any choice you make, there are some very distinct drawbacks to staining as well. Understanding what can possibly go wrong with the process can help you to avoid potentially costly mistakes down the road.
Here are some of the cons to staining that any homeowner should be aware of before they proceed:
Accentuates sanding marks – Sanding is a necessary step in order to prepare your hardwood to accept stain, but when done incorrectly it can leave a series of scratches and gouges in the wood.
When stain is then applied to that wood surface, the pigment in the stain seeps into all of those fine marks, showing up darker in those areas and making them stand out even more. The result can be a murky and busy overall look.
Not all woods are meant to be stained – There are certain types of wood, including maple, birch, and pine, that don’t take well to stain. These woods are very tight-grained, meaning there are very few openings into which the stain pigment can settle and provide coverage.
At the same time, pine and other coniferous woods also contain sap, which will actively resist stain. Staining these types of woods can result in areas of beading where the stain is repelled, making for a messy look.
Tendency for “bleedback” – Unlike paint, stain cannot be corrected or darkened by applying more layers. No matter what type of wood you choose, it can only absorb a certain amount of stain. Once it reaches its limit if you continue to apply the stain it will simply rise back up to the surface, resulting in what is known as “bleedback”.
The same effect can happen if you go over a layer of stain with a layer of finish that is not compatible. In either instance, you’ll be left with unsightly pockets of beading and spotting that will mar the overall look of your floor.
Staining is a very time-consuming process – one of the biggest drawbacks to staining, and one that is very often overlooked by homeowners is the sheer amount of time the process can take.
If a stain coat is not completely dry it won’t be able to accept a layer of finish and if the stain and finish do not bond the finish can smudge and even peel off entirely. The only recourse will be to sand the floor again and start over.
In order to dry thoroughly stain requires a minimum of 48 hours in the ideal conditions of heat, humidity and air movement. Since it can be difficult to achieve those ideals in most cases, you’re more likely to need at least 72 hours for your stain to dry.
Even the slightest variation in temperature, humidity and air movement can have a drastic effect on the ability of your stain to dry properly. Once the stain is dried, then you’ll need to apply a finish coat and wait for that to dry as well, all of which can mean up to a week or more for the entire process to be completed.
Staining vs. Clear Coating
When it comes to achieving the perfect look for your hardwood floors, staining isn’t the only option. If you want a more natural, rustic look that emphasizes the inherent grain and pattern of the wood, you could always opt for a clear coat finish. Unlike staining, clear coating doesn’t add any pigment but simply enhances the existing look of the floor.
This can have its advantages, most notably that it allows for greater reflection of light, which can help to add depth and a feeling of size to smaller rooms. This is particularly noticeable in rooms with a lot of windows that allow for more light.
Another advantage of clear coating is that unstained floors can provide an effective accent to darker wood accessories such as trim and furnishings. This interplay of various shades of wood can add extraordinary depth to a room which many designers find particularly appealing.
What’s the Bottom Line?
Whether you are installing new floors or working with existing hardwood, staining is an extremely important part of the process and one that should be approached with great care.
When done properly it can enhance and reflect the beauty of the wood and help to pull together the overall design of the room, but even the slightest misstep in this process can cost a considerable amount in time, effort and money.
Before you decide to stain your wood floors, it’s important to understand everything that is involved in the process and get expert input so that you can be sure you are making the right choice and getting the final result that you’re looking for.
With the right choice, either stain or clear coat, you can enjoy all of the many benefits that a beautiful hardwood floor can bring to your home.
Having a Hardwood Floor Installed? Here's What to Expect
Having a hardwood floor installed can be a big project, but with the right preparation and understanding of the process, it can go smoothly. Learn what to expect and how to prepare for a hardwood floor installation.
Nothing compares to the look and feel of a hardwood floor, which is why hardwood is such a major selling point in the real estate market. Many people opt to install new hardwood floors in their homes or replace existing ones if they become damaged.
While the beauty of the finished product cannot be denied, the installation process can be quite an undertaking and homeowners need to be prepared for all of the steps involved and any possible complications that may arise. The better you understand the entire process, the more you’ll be prepared to handle it all, and the more smoothly it can go for you and your family.
Here’s what to expect when you have hardwood floors installed in your home.
Choosing Your Floor
The first step in the process is choosing your flooring. The type of wood and finish that you choose can affect the amount of time involved in the overall installation process. Some woods are harder than others and may take to stains and finishes easier, meaning the amount of time required for those steps may not be as long.
The size and layout of the room where the floor is being installed can also make a difference. The larger the floor and the more complicated the layout, with lots of intricate corners and edges, the more labor-intensive the installation is likely to be. You should be sure to talk through all of these things with your contractor before installation to make sure that you have the most accurate possible estimate of the time and expense involved.
Preparing The Room
Once you have chosen your flooring and finishes, the next step is preparing the room for installation. This will necessitate removing all furnishings, rugs, and draperies as well as anything hanging on the walls. That way the flooring team will have all the room they need to move and you will be able to minimize the potential damage to your belongings.
Since installing hardwood requires several rounds of sanding, there will be quite a bit of sawdust produced, and by removing your belongings from the room you can prevent them from becoming covered in dust.
You’ll want to keep all pets out of the room and you and your family will also have to stay off the floor and may even need to be completely out of the house for a day or two during installation, depending on the type of finish that is used.
The amount of preparation required before installation can also vary depending on the status of your home. In new homes, the house should be finished up to the drywall stage, with windows and HVAC system installed and operational for up to a week so that the home can be brought up to normal livable temperature.
Whether the home is new or not, the flooring material will need to be delivered about three days before installation so that it can acclimate to the temperature and humidity level of the home.
Installing The Floor
Once everything has been prepared, the installation itself can begin. Again, this can be an intricate process, depending on the condition of the subfloor of the room. As the wood is attached directly to the subflooring, any discrepancies in the subfloor can affect the overall look of the finished floor. It may be necessary to remove glue and previous flooring if hardwood is being replaced.
In new homes, the floor may have to be floated to ensure that it is level. Since wood can expand and contract over time, particularly in weather extremes, leveling is always a concern with hardwood floors. The more care that’s taken to ensure levelness during installation, the more likely it is that the floor will stay level over time.
Sanding The Floor
Once the floor is installed, it will then be necessary to sand it. Sanding helps to prepare the boards to take the finish coat and can also help to ensure flatness and smoothness. While the levelness of a floor is dependent on the physical makeup of the subflooring, the terms “flatness” and “smoothness” apply to the sanding and indicate how smooth and even to the touch a floor is after sanding.
The goal for any installation is to end up with a finished product that is as smooth and even as possible. It will often require several rounds of sanding before the ultimate result is achieved.
Applying The Finish
After the floor is thoroughly sanded, it’s time to apply the finish coat. A finish is a clear topcoat that is applied in order to protect the wood from everyday wear and tear. There are different types of finishes available and the type you choose can depend on a number of factors, including the type of wood you’re using, the traffic pattern in the room, and the environmental conditions.
Some types of finish have stronger fumes than others and may also take longer to dry and this will indicate how much time will be required before you can use the room or even be in the home itself. The general recommendation is to wait at least 1-2 days after installation before walking on the floors.
You should also wait to replace rugs and furniture in the room until the finish is completely dry and the floors have settled. You may need to wait as long as 30 days before placing any rugs to avoid causing spots to form.
The Final Product
Since wood is a natural substance there are likely to be some imperfections in the finished product, such as whorls, knots, and grain lines. These can vary depending on the type of wood used and should be considered a part of its natural beauty.
It’s also important to remember that the installation process is a manual one, so it may result in a “handcrafted” final appearance, with buffer swirls, sanding marks, and other markings. Again, this should all be considered part of the unique look of hardwood flooring.
Finally, you need to realize that no two hardwood floors are exactly the same. No matter how careful the installation process is, the ultimate durability and performance of your floor will depend on the traffic pattern of your household and the softness of the wood itself. The softer the floor, the more likely it will be to display scratches and dents over time.
With all of this in mind, you should be well prepared to experience the installation process and ready to handle all of the various steps with ease. If you have any specific questions, you should always discuss them with your contractor before the job begins. With the right approach to installation, you and your family will be able to enjoy your beautiful hardwood floors for many years to come.
White Oak vs. Red Oak: The Flooring Facts
White Oak and Red Oak are two of the most popular hardwood flooring options, but they have different characteristics and properties. Learn about the differences and decide which one is the best fit for your home.
Hey everyone, it's Patrick here kicking off yet another little flooring blog fiesta! Today, I had a brilliant lightbulb moment – I dove into the treasure trove of your favorite blog posts throughout the years, and guess what? This one's been a superstar! So, hold on to your flooring samples because I've jazzed it up with fresh facts, snazzy information, and some pro insights from yours truly. Let's embark on this journey together and dive into the fascinating world of hardwood flooring. Cheers to an upgraded and oh-so-2023-24 blog post – hope you're ready for a flooring adventure like never before! 🚀
White Oak vs Red Oak The Flooring Facts Decoded and updated
When it comes to choosing a hardwood floor, many people immediately think of oak. It’s a good choice as oak is one of the most durable types of woods as well as one of the most readily available. With the right installation and finish, oak can provide you a beautiful floor that can last more than 100 years. However, the age-old debate between white oak and red oak continues to perplex homeowners. Both types of oak flooring boast their unique features, making them desirable choices for various settings. But how do you decide which one is best suited for your needs? In this blog post, we will unveil the key differences between white oak and red oak flooring, guiding you through aspects such as color variations, grain patterns, hardness, water resistance, and cost. By the end of this, I anticipate that you will possess the knowledge needed to make an informed decision when choosing the ideal flooring for your home.
Key Takeaways
White oak and red oak flooring have distinct characteristics in terms of color, grain pattern, hardness, and water resistance.
White oak is harder than red oak, with slightly higher levels of coloring differences. Both require finishes for added protection.
Consider factors such as cost, design preference, and appropriate finishes when selecting between white oak or red oak flooring to ensure long-term flooring durability in your own home.
Where does oak come from, and what is it?
As a homegrown wood forested throughout the U.S., oak is considered more environmentally friendly as it has a much lower carbon footprint than more exotic woods. What is less well-known about oak is that there are actually two distinct types of oak flooring that you can install in your home: white oak and red oak.
While most instinctively choose White Oak, it may be worth your while to consider Red Oak, which can often be a more affordable and attractive option. Pricing usually plays a significant role in the decision-making process for homeowners when deciding between these two woods. It goes without saying that usually, you can find a better deal on these flooring products by visiting distributors and big box stores in person. However, I have pasted some Amazon links here to help you find some better flooring products online for those living in more rural areas.
Completely raw, unfinished Red Oak flooring
Unveiling the Characteristics of White Oak and Red Oak Flooring
White oak and red oak are the two species of oak wood commonly used in hardwood flooring. While they share some similarities, the main distinct differences between the two of them are in:
Color
Grain pattern
Hardness
Moisture susceptibility
Both types of oak flooring bring unique charm and character to your living space, we should examine these characteristics more thoroughly to better comprehend their individual attributes.
Color Variations in White Oak and Red Oak
Color differences between White Oak and Red Oak Flooring
One of the most noticeable differences between white oak and red oak flooring lies in their color variations. White oak flooring exudes hues of medium brown and tan, while red oak boasts tints and subtleties of red and pink. Both types of oak flooring accept stains well, but their staining capabilities differ. Red oak tends to turn a more distinct reddish shade when stained. White oak, on the other hand, generally darkens to a brown hue.
Despite their initial difference in color, as you apply stain to them that difference is diminished. In fact, with any stain darker than medium brown, the difference is almost indistinguishable unless side by side. This can be an important factor when you consider overall pricing, as it may not be necessary to pay the extra amount for white oak when you can easily get the same effect with red oak for less money.
No matter what oak you are choosing to go with, I highly recommend finishing the floors with a very natural and light appearance. This will better show off the wood that you have, and the lighter color will also make your space seem much bigger as well. A natural finish can further enhance the hue of each type of oak. However, a dark stain can have wonderful benefits too. A dark stain color can help blend the red & white oak together if you are stuck in a situation with two varying wood species inside of the same home. When finishing with a light appearance, the red oak will become more pink or reddish, while the white oak with tighter grain lines will darken and become more honey-blonde. However, if stained, the differences become more minimal the darker that the color gets. This flexibility allows you to experiment with finishes and stains to achieve your desired look and match the existing color palette of your home.
Mixed species flooring that includes red & white oak. Stained a very dark Ebony color & finished with Loba Invisible.
Grain Patterns: A Close Look
The other factor that can visibly distinguish one flooring from another is the grain pattern of the wood. While both are obviously oak, there is a definite difference between the look of White Oak and Red Oak based on the graining.
White oak exhibits a more consistent grain pattern with delicate color variations.
Red oak showcases a more pronounced grain pattern with darker hues in certain regions.
Rays, the small dark lines present in the tighter grain pattern of oak flooring, provide it with a unique character.
The cut of wood is an important choice when considering a floor made of red oak or white oak. Standard select & better red oak and white oak floors come with a mixture of plain sawn, rift-sawn, and quartersawn boards. Rift and quartersawn oak floors exhibit a distinct appearance, which many customers specifically request. While both red oak and white oak floors can be rift and quartersawn, it is more common in white oak floors.
Rift & Quartersawn White Oak floor, fully finished with Loba Invisible
As you can see, when perfectly quartersawn, the grain pattern of red & white oak flooring differs. White oak has more discernible rays and looks more uniform, while red oak’s grain has more variations, swirls, deviations, and can sometimes look uneven in appearance. Grain patterns not only contribute to the visual appeal of your flooring but also impact its durability and resistance to wear and tear.
Hardness Comparison: Janka Ratings Revealed
The Janka scale is a measure of the hardness of wood and is utilized to compare the hardness of different species of wood. White oak has a hardness rating of 1360, while red oak has a rating of 1290, making white oak generally considered harder than red oak. This difference in hardness translates to a higher resistance to wear and tear for white oak flooring, contributing to its durability. Mainly, this harness difference helps combat against DENTS in your hardwood flooring.
So far, when comparing red oak vs white oak, there are several advantages to white oak:
It has a higher hardness rating, making it more resilient and resistant to wear and tear.
This makes it a better choice for high-traffic areas of your home.
Its tighter grain makes it less prone to wear and tear.
However, because of this tight grain, it is also more prone to splintering, and as we’ve mentioned the white oak is more expensive.
The hardness and durability of each option should be taken into account when making a choice between these two different wood types. Here’s a quick recap of factors to consider:
White oak may be slightly harder and more resistant to wear and tear, but because of this tight graining, it can have more splintering in the finished product.
Consider the desired appearance of the flooring. Do you want a dark floor? Then don’t waste money on White Oak. Do you want a natural floor? Or perhaps a rift and quartersawn floor? Then definitely consider the white oak flooring.
Take your budget into consideration.
It’s important to weigh these factors against each other to make the best choice for your own personal needs.
Red oak flooring refinished using a nice light stain, in order to mimic the look of white oak.
Mixing and Matching: Can You Combine White Oak and Red Oak Floors?
If you’re adding wood flooring to a home that already has wood touches, including stair treads and banisters, you’ll want to find something that is a good match so that all of your wood has a unified look. Although the idea of combining white oak and red oak floors in one project might be appealing, keep in mind that they are not interchangeable. The color difference between the two types of wood floors is noticeable when they are side by side, making it difficult to achieve a cohesive look. In very small situations, the color difference between the two types of wood floors is less noticeable if they are stained a very dark color.
Funny enough, years ago when I was still young and starting out, I documented a project where the homeowner purchased their own materials. Unfortunately, they purchased incorrect wood before hiring us. They purchased white oak flooring for their red oak flooring project. Because it was a flip home, and the timeframe was a huge issue, the homeowner had us install, sand, and finish the floors anyway. So, I’ve got some pictures for you of what a color difference between red and white oak might look like that I think will be very helpful. Before a dark stain, and after a dark stain.
This is a white oak floor tied into a red oak floor. As you can see, the red oak is on the top and the white oak is on the bottom. The difference should be VERY clear when raw.
This is the same exact floor from the same exact angle after being fully finished with a dark stain. Pretty hard to tell, huh?
Now, after taking a look at these two pictures, it raises an interesting question. Considering a dark stain, would you still opt for white oak, even with a $3+ per square foot difference in price? It's essential to navigate through various perspectives, and sometimes, the advice from contractors & designers may not align perfectly with the desired outcome or budget. I've come across numerous projects where there was a strong preference for white oak from the interior designer, only to discover later that the final finishing color was ebony...facepalm. It emphasizes the importance of clear communication and understanding individual preferences in the floor decision-making process.
It’s also worth remembering that Red Oak is much more frequently used for surfaces like stair treads and handrails so if you’re trying to match existing wood and you have to guess, you’ll probably want to go with red oak. If you have a stair project coming up and are looking for material, these stair treads are actually insanely well-priced. They’re great too because they have a nice, new, square nosing piece. Instead of the very commonly rounded over piece which looks way more traditional.
Water Resistance: Which Oak Stands Strong?
When installing a hardwood floor in your home, the potential for water damage is always a concern. As a closed-grain wood, White Oak tends to be more resistant to water damage, which is why it is often used for boat building.
Despite the differences in water resistance between white oak and red oak flooring, it is essential to note that neither type of oak can resist water damage entirely. The finish on top of the floors is crucial for water resistance, as it provides an additional layer of defense against water and other liquids. Some options for finishes include:
Water-based finishes: These offer better spill resistance to water and chemicals.
Oil-based finishes: These also provide good spill resistance.
Hardwax oil finishes: These can be more susceptible to spills and water due to a thinner film layer on top.
If high levels of water and moisture are a huge concern, consider a quartersawn floor, whether it be red or white oak. A quartersawn floor has much tighter graining, as we discussed before, which actually makes it considerably more stable in climates with higher heat & moisture levels. Whether you install a red oak quartersawn floor or a white oak quartersawn floor, the fact that it is quartersawn will make a massive difference in stability and resistance to movement\moisture.
Evaluating the water resistance of your oak flooring involves considering not only the inherent water resistance of white oak or red oak, but also the significant role of finishes in protecting against moisture damage. Properly finished and maintained oak floors can provide a beautiful and durable addition to your home, regardless of the specific type of oak chosen.
Cost Analysis: White Oak vs Red Oak Flooring
Well, here we are. The big question and the main section that most of you are probably here for. In addition to their distinct characteristics, white oak and red oak flooring also differ in cost. White oak is typically more expensive than red oak, with the average cost per square foot for white oak flooring ranging from $5.00 to $12.00 depending on where you are located and depending on the exact type of floor you want. This higher price point can be attributed to factors such as white oak’s current trendiness and its status as a designer favorite.
Red oak, on the other hand, is a more budget-friendly option given the current prices. Red oak usually does not exceed past $4-8 dollars per square foot depending on the exact type of flooring you want and where you are located. As a result, homeowners working within a tighter budget may find red oak flooring to be a more feasible choice. However, it’s crucial to consider the long-term value of your flooring investment, as factors such as durability and water resistance can impact the overall cost-effectiveness of each option.
It is important to balance your budgetary constraints with your desired aesthetic, durability, and other factors when considering the costs of white oak and red oak flooring. While white oak may be more expensive upfront, its higher hardness rating and water resistance can contribute to a longer-lasting and more resilient floor, potentially saving you money on repairs and replacements in the long run. However, it’s important not to blow your entire budget on just the flooring material. You must remember to properly balance things as the sanding and finishing products are a HUGE cost factor that will contribute to your project budget as well.
Making the Right Choice: recapping the proper Factors to Consider
Choosing between white oak and red oak flooring involves a careful evaluation of various factors, including:
Color
Grain pattern
Hardness
Style
Cost
Your personal preference and the desired aesthetic for your living space will play a crucial role in determining which type of oak flooring is best suited for your needs.
For instance, if you prefer a more consistent grain pattern with delicate color variations, white oak may be the better choice. On the other hand, if you find the pronounced grain pattern and reddish hues of red oak more appealing, or the price, then red oak flooring may be the ideal option for your home. Arguably, if water resistance and durability are top priorities, then white oak’s higher hardness rating and water resistance may make it a more attractive choice, even for a higher price point.
The choice between white oak and red oak flooring hinges on a balance of factors such as budget, desired appearance, and specific requirements for your living environment. By carefully considering each aspect, you can make a well-informed decision and invest in oak flooring that will not only enhance the beauty of your home but also provide a durable and long-lasting surface for years to come.
Tips for Maintaining Your Oak Floors
Appropriate maintenance is vital for preserving the longevity and beauty of your oak floors, whether you opt for white oak or red oak flooring. To keep your floors looking their best, it’s essential to follow proper cleaning practices and use recommended products.
Primarily, steer clear of using harsh chemicals or abrasive cleaners on your hardwood floors, as these can harm the finish. Instead, use only water-based floor cleaning products, such as Bona hardwood floor cleaner and Loba hardwood floor cleaner, or a homemade solution of vinegar and water. Be sure to avoid products that contain wax, as well as products like Murphy’s soap and oil or mop and glow, which can leave a residue on the floor and cause big issues in the long run.
Beyond using appropriate cleaning products, maintaining a regular cleaning regimen that includes frequent sweeping and vacuuming to eliminate dirt and debris from your floors is important. Placing mats and rugs in high-traffic areas can also help protect your oak floors from damage. By following these maintenance tips, you can preserve the beauty and durability of your oak flooring for years to come.
Conclusion
Well if you’ve made it this far, kudos to you for making it to the finish line! Big thanks for sticking with me through this oak-tastic journey. In a nutshell, deciding between white oak and red oak flooring is like choosing the perfect dance partner – it all depends on the music! Factors like color, grain, hardness, water resistance, style, and cost all strut their stuff on this parquet dance floor.
So, here's the grand finale: by shimmying through these considerations and tuning into your personal rhythm, you're set to make a flooring decision that's not just a choice but a dazzling performance. Whether you're team white oak or red oak, the backstage secret is proper maintenance – keeping that dance floor in tip-top shape for an encore performance.
Before the curtains close, I want to express my heartfelt gratitude for your unwavering support over the past 12 years. It hasn’t been easy finding time to put quality posts like this together while also running my actual flooring business. But, you’ve all been here, always reading and supporting anything that I put out. For that, I thank you greatly. Here's to more exciting blog posts and flooring adventures in the future. And guess what? I've got a brand-new post hot off the press this year, spilling the tea on whether you should stay put during the polyurethane finish drying process. Spoiler alert: it's a must-read! Thanks again, and keep rocking those floors, my friends!
Rough sanding a mixed species floor that includes red oak and white oak.
Frequently Asked Questions
Is red oak or white oak better for flooring?
White Oak has a slightly higher Janka hardness rating compared to Red Oak, making it the better option for flooring in terms of resistance to dents and scratches.
What are the disadvantages of white oak flooring?
White oak flooring can suffer from splintering and cracking if not properly maintained due to its very tight graining, but its stylish look and durability make it a great choice for many homes.
What are the advantages of red oak flooring?
Red oak flooring is an industry benchmark due to its easy stainability, ease of sanding, and unique wide-grain pattern. It can easily be finished and stained without blotching and sanded with a pad or block. It is also considerably less expensive than white oak.
What is the visual difference between red and white oak?
Red oak has pink undertones, whereas white oak has more tan and brown tones. White oak is usually darker in color than red oak.
Can I combine white oak and red oak floors in a single project?
Combining white and red oak floors in a single project is possible, but never really recommended unless it is an emergency. Caution must be taken when selecting finishes and stains to make the colors complement each other. Very dark colors are required if mixing the two species of wood together.
Water Based Finish vs Oil Based Finish: Myths and Comparisons
Water-based finish and oil-based finish are two popular options for hardwood flooring but have different characteristics and properties. Learn about the myths, comparisons and decide which one is the best fit for your home.
Most homeowners agree that nothing can beat the rich, warm look of hardwood floors. In order to achieve that look, and more importantly to preserve it through years of use, it is necessary to apply a layer of polyurethane finish.
While the basic purpose of polyurethane finish is to protect your floor, that doesn’t mean all finishes are created equal. There are two distinct types of finish, oil-based and water-based, and there are some distinct differences between the two that you’ll want to take into consideration before you choose a finish for your floors.
Drying Time
No matter which type of finish you choose it will be necessary to apply several coats in order to provide the right amount of protection for your hardwood flooring. This is a crucial point to bear in mind because the most significant difference between an oil-based and a water-based finish is drying time.
Since water-based finishes are thinner, they tend to dry much faster and therefore you can apply several coats in one day. You’ll also be able to walk on the floor within about 4-6 hours after the final coat is applied, which means that you could be using the room again in the same day.
Compare that with thicker oil-based finishes that generally take at least 12 hours for each single layer to dry and require 24 hours of wait time after application of the final layer before you can walk on them. That means the room being worked on will not be usable for several days, which can be a major headache for homeowners.
Common Myth: Taking longer to dry means your floor will have better, stronger protection.
While oil-based finishes can certainly provide plenty of protection that doesn’t mean that water-based finishes are less effective. Water-based finishes may dry faster but they still provide a barrier to deflect scratches and dents and keep your floors looking beautiful for years to come
Smell
When most people think about applying a finish to hardwood floor the first thing that comes to mind is the strong smell. Unfortunately, there’s no way to completely avoid the pungent odor that is characteristic of polyurethane finish, but it can be mitigated to some degree by using a water-based finish. In fact, most water-based finishes have very little smell, making them safer to apply and safer for your family to live with.
When applying the much stronger-smelling oil-based finishes, you’ll need to use a respirator and you’ll find that the smell remains on your clothes for hours afterward.
It is highly recommended that you and your family leave the house for the duration of the finishing process and that you remove your pets from the home as well. With water-based finishes, there is no need to use a respirator and it is perfectly safe for your family and your pets to remain in the house.
Of course, the real safety issue here is not just the smell, it’s the fact that flooring finishes contain VOCs (volatile organic compounds), which are emitted into the environment and can cause a number of health issues.
In general, water-based finishes contain fewer VOCs than oil-based finishes, which makes them more attractive to consumers who are worried about being environmentally friendly.
Common Myth: Fewer VOCs make water-based finishes the obvious environmentally friendly choice.
While having fewer VOCs is certainly a selling point, it doesn’t necessarily mean that water-based finishes are the clear choice for the environment since they don’t last as long as oil-based finishes and will therefore need to be re-applied more frequently. Depending on the wear your floor gets, this could negate any benefit you’re getting from the lower VOC content.
Thickness/Hardness
Since a finish is applied in order to protect the wood underneath, the thickness of that protective layer is certainly an important point to consider. Not surprisingly, the thickness of the finish layer varies depending on how many layers of finish are applied.
As water-based finishes are thinner, more layers may be required in order to achieve the desired level of protection. This will depend on the area being finished and what the traffic patterns are. In rooms that see a lot of traffic, a heavier finish will provide extra protection.
Common Myth: Since it’s thicker, an oil-based finish provides more protection.
Since the extra thickness of an oil-based finish helps to prevent surface scratching, that makes it a good choice for high-traffic areas but it doesn’t mean that it will protect against all damage. While they may be thicker, oil-based finishes are also softer than water-based, which means they are more susceptible to denting.
In a room where heavy pieces of furniture are used and moved, a water-based finish may actually be the better choice.
Cost
Let’s face it, for any homeowner on a budget cost is going to be a primary concern and it is one of the areas where oil-based and water-based finishes differ dramatically. Simply put, water-based finishes are significantly more expensive than oil-based.
You can pay as much as $0.50 to $1.00 more per square foot for a water-based finish than you would for an oil-based finish. When you also consider the fact that water-based finish wears out more quickly and will need to be re-applied more often, you can see how your costs could go up even more.
Common Myth: Paying more means you’re getting a better end result.
While in most cases, paying more usually means getting a higher quality product this isn’t always the case for flooring finishes. There are many very good quality oil-based finishes that can give you the look you want for much less. If you’re on a tight budget you’ll want to carefully consider all of your options and make the choice that works best for you.
Look
When it comes to flooring finishes perhaps the biggest deciding factor is the end look. You don’t want to go to the expense and effort of installing hardwood flooring only to end up with a less-than-ideal final product. The final look is also where oil-based and water-based finishes differ the most.
Oil-based finish has an amber, or yellowish, color while water-based finishes are clear. Obviously, since they don’t have any color of their own, water-based finishes won’t add any extra color to your flooring.
That means the beautiful natural look of the wood will able to shine through for the duration of the floor’s life. In comparison, oil-based finishes will darken over time, causing the floor to look darker and heavier.
Common Myth: Oil-based finish produces a richer, warmer, more attractive look on all types of flooring.
While an oil-based finish can help to enhance the look of many types of hardwood floors, it doesn’t necessarily produce the best final look for all types of flooring. Since it tends to get yellower over time, it is not recommended for woods that are lighter in color, including gray-stained, white-stained, or white-washed flooring.
Also, lighter woods like Maple and woods with a naturally yellow tint of their own such as Ash, Pine, or Fir, usually do better with a clearer water finish that won’t take away from their natural look. With harder woods like Oak, an oil-based finish is the better choice as the addition of the amber tint can help to produce a warm, rich look.
Bottom Line
As you can see, a good case can be made for either an oil-based or water-based finish. Both are perfectly legitimate choices and each one has its pros and cons. The finish you choose for your flooring will depend on the type of wood you use, the area where you’re using it, and the overall look you are trying to achieve.
There is no doubt that hardwood flooring can be a significant investment so you should carefully consider your options before you choose a finish. That way you can protect and enjoy your beautiful floor for years to come.
Why Hardwood Flooring is a Much Better Choice Than Laminate
Nothing can add to the aesthetic appeal of a room like a good floor, and when it comes to flooring nothing quite matches the appeal of wood. For many homeowners and designers alike, a wood floor is the mark of true quality and can increase a home’s value dramatically.
Because hardwood flooring can be expensive, many people choose laminate instead. However, in most cases it’s not the best choice. Let’s take a look at some of the reasons why you should always opt for hardwood.
Composition
One of the easiest ways to see the benefits of hardwood over laminate is by looking at the composition of both. Hardwood flooring, as its name suggests, is made up of individual planks cut from a larger piece of wood and then milled to their final size and shape. In general, hardwood planks are three-quarters of an inch thick, giving them much more substance than laminate. Since they are made from one solid piece of wood, hardwood planks are sturdier and more substantial, meant to last a lifetime.
The composition of laminate is more complicated, involving several layers, the thickest of which is a core made of fiber board, a much flimsier material than wood. Surrounding that core are several different layers meant to simulate the look of wood, provide waterproofing and guard against scratching. Not only does this make laminate less substantial than solid wood, but it can also lead to other dangers from the various chemicals used to treat it.
One of those chemicals, formaldehyde, has been the focus of much controversy in recent years. Lumber Liquidators, one of the largest flooring retailers, became the subject of a lawsuit when it was determined that some of its laminate flooring, which had been manufactured in China, contained dangerous levels of formaldehyde.
Scientists have proven that prolonged exposure to fumes from formaldehyde can lead to serious health issues and may be particularly dangerous for individuals who suffer from respiratory ailments like asthma. Lumber Liquidators stopped carrying the flooring in question in response to the suit but the case definitely brought much needed attention to the potential dangers of the chemicals used in manufacturing laminates.
Installation
Another key area of difference is installation. With specialized seams that click together, one of the main selling points of laminate flooring is that it is easy to install. While this is generally true, the tight connection of laminate boards can be troublesome as it doesn’t allow for the natural expansion and contraction that happens over time.
Most hardwood flooring is made with tongue and groove or shiplap design, allowing the boards to overlap but also allowing room for the wood to breathe, which makes it more adaptable to expansion and contraction. At the same time, prefinished hardwood often comes with edges that are slightly beveled at the top of the plank. When they are connected, this beveling leaves a small V shape between the boards, which adds an extra sense of dimension to the overall look, making it more aesthetically pleasing.
Finish
In terms of design, the finish of a wood floor is probably the most important quality of all and once again, there is a distinct difference here between hardwood and laminate. Laminate flooring is manufactured with what is called a photographic layer, which is embedded with a photographed image of stained wood. By using different types of woods and different colorings, you can find a laminate to match any room design. Likewise, there are prefinished hardwood planks that come already stained and sealed in a variety of colors and styles.
For designers and homeowners who want to customize to their taste, using unfinished hardwood can provide an even more desirable option. Since these planks come without any stain or finish, they can be customized to your liking to fit a specific design style. While this involves the extra work of staining and sanding, to many people it is well worth the effort to get the exact look they want.
Durability
As anyone who has ever lived with a wood floor knows, damage is a fact of life. It’s nearly impossible to escape the occasional dent or ding or spill and depending on the location of a room, fading from the sun may be an issue over time too. With all that in mind, you can’t easily deny the durability of hardwood. Again, as the name suggests, it is hard and that helps it to stand up to the test of time. Hardwood floors are made to last, which is why most realtors consider them one of the biggest assets of any home.
This doesn’t mean that they can’t be damaged. High traffic areas will eventually show wear and tear and dropping an item on a hardwood floor can cause a ding, but these common issues can be more easily repaired with hardwood than laminate. A simple sanding and buffing will usually be all that is needed, while individual planks may need to be replaced when laminate becomes damaged.
Of course, the one threat that even durable hardwood can’t always stand up to is water. Water damage can cause expansion and buckling with hardwood floors, which can become both an eyesore and a tripping hazard. In areas like basements, kitchens and bathrooms, where contact with water is more common, laminate is generally the preferred choice as it doesn’t stain as easily.
You can protect against water and humidity issues by choosing wood of a higher quality that will stand up to water better and by allowing wood planks to acclimate before installing by leaving them in open boxes at the construction site for several days before installation. Even with acclimation, however, water will always remain a major concern with any kind of wood flooring.
Bottom Line
While hardwood flooring can be more costly and more difficult to install, there is no comparison when it comes to durability and the warm, natural feeling of wood. Though the manufacturers of laminate have made great strides in providing a product that approximates the look of wood, the reality of laminate is that it is less durable and has a more artificial look as well as containing potentially harmful chemicals that could adversely affect your family’s health.
Not only can you customize untreated hardwood with your own choice of stain, allowing it to match any design aesthetic, as a natural, chemical free, product it is the safer option by far. The beauty, durability and safety of hardwood speak for themselves. Taking all these factors into account, it is easy to see why hardwood is by far the better choice.
Rubio Monocoat - Rustic is the New Sleek
If you’re discussing flooring options with a Chicago floor refinishing company, something you may want to consider is Rubio Monocoat. This floor refinishing option offers many advantages, both in its unique appearance as well as its durability.
Rubio Monocoat is also a safer and more environmentally sustainable choice for your home. So as you consider all of your hardwood floor refinishing options, let’s see if a Rubio Monocoat floor is the right choice for you.
What is Rubio Monocoat?
Rubio Monocoat is one of the newest floor refinishing options out there. Unlike typical stains that get painted onto the top of hardwood flooring, Rubio Monocoat is a plant-based hard wax oil finish. A Rubio Monocoat finish will penetrate deeper into the wood, creating what is called a “super matte” finish that is quite unique.
It is also much more environmentally sustainable than other flooring stains since it is plant-based. Moreover, it also does not emit any volatile organic compounds (VOCs) either, another benefit of this new, high-tech hardwood floor refinishing option.
Why Rubio Monocoat May be a Great Choice for You
One of the best reasons to choose a Rubio Monocoat floor is because of its beauty and uniqueness; there is truly nothing else out there that looks like a hardwood floor refinished in Rubio Monocoat. The rustic yet sleek appearance of a hardwood floor with hard wax oil applied to it can really add the Wow Factor to your home.
Additionally, if you’re concerned about the environment and the safety of the hardwood floor refinishing options you’re considering, there is no better choice than Rubio Monocoat. Finally, if you’re focused on things like your home’s resale and property value, it is hard to argue against this high-tech hard wax finish.
Rubio Monocoat is new, however, so it can be challenging to find floor refinishing companies in Chicago that are using it. Consider contacting companies like Hardwood Flooring Glencoe or Lakewood Floor Refinishing, or find another reputable company that is ready to work with the product. Once you find a good hardwood floor refinishing company in Chicago that is familiar with Rubio Monocoat, you’ll be ready to take the flooring in your home to the next level!
Hardwood vs. Softwood Flooring: What is the Difference?
Hardwood and softwood flooring are two different types of wood that are commonly used in flooring, but they have different characteristics and properties. Learn about the differences and decide which one is the best fit for your home.
Wondering about the difference between hardwood vs softwood? If you’ve shopped around at different flooring companies in Chicago, you already know there are a lot of flooring choices out there. When you’re getting ready to choose a wood floor, one of the biggest choices you’ll have to make is whether to install hardwood or softwood flooring.
Each type of wood flooring has its advantages and drawbacks, which you’ll need to understand to make an informed decision about your floors. So, let’s take a close look at hardwood versus softwood flooring, so you know the difference between these two wood choices.
Softwood Flooring
Softwood flooring comes from evergreen trees such as pine, spruce, cedar or fir trees. Softwoods have a lighter color than most hardwood flooring choices, and a looser grain. Most softwood flooring choices are more prone to wear and tear from pets’ nails, heels, and scratching than their hardwood counterparts, so they may not be a good flooring choice for busy families.
You will definitely need the name of a good Chicago floor refinishing company if you decide to go with softwood flooring! However, since many softwoods have a fine, clean appearance, they could be good choices in rooms that will expect less foot traffic. Additionally, because softwoods are a faster growing, more prevalent form of timber, they often cost less than hardwoods.
Hardwood Flooring
Hardwood flooring comes predominately from deciduous trees like oak, maple and hickory. Hard wood floors come in a wide variety of colors and styles, and tend to have closed grains. Because the hardwoods vary in appearance so much from one another, they offer homeowners a tremendous amount of options.
True to their name, this flooring is more durable than softwoods and can hold up to considerably more wear and tear. However, the slow growing hardwoods are in greater demand, and are usually the more expensive choice when it comes to wood flooring.
There are considerable differences between hardwood vs. softwood flooring. As you begin discussing options with your hardwood floor installation company in the Chicago area, make sure you consider your current lifestyle and budget, so you can make the best flooring choice for yourself. Good luck!
Contact Plus Hardwood Flooring today for a free estimate!
4 Types of Hardwood Flooring and When to Choose Each
There are four main types of hardwood flooring: solid, engineered, laminate and bamboo. Each type has its own unique characteristics and is suited for different types of applications and environments. Learn about the different types of hardwood flooring and when to choose each one.
If you’re in the Chicago area and thinking about types of hardwood flooring, you have many different options. So, which one should you choose? Hardwood floors are an important part of your home, and if you make mistakes in selecting them, it could end up costing you in the long run.
So, before you call a Chicago hardwood flooring company, do a little research so you get those floors right.
Here are four types of hardwood flooring and some thoughts about when to choose each one.
Oak Hardwood Flooring
Oak is one of the most common choices for hardwood flooring that homeowners make, and it is understandable why. It has medium to heavy grains and a beautiful undertone that many people describe as rosy, particularly red oak.
Oak is a great choice for homeowners with big families since it is durable and can take a beating without showing too much wear. Oak tends to be less expensive than other types of hardwoods too, which is another plus.
However, because it is so common to find oak floors in homes these days, some prospective homeowners prefer other, rarer hardwoods for their floors.
Maple Hardwood Flooring
Maple is another popular type of hardwood flooring, although it is not quite as common as oak. Like oak, there are many different maple flooring options available to homeowners. The tone of maple flooring is generally lighter than other hardwoods, so it is a great choice for contemporary or modern homes.
Maple is also fairly tough as well and will hold up with minimal dents and nicks. However, Maple is also more difficult to finish than other types of hardwood flooring and can react poorly if it is exposed to extended periods of sunlight.
You’ll definitely want to have a discussion with a trusted hardwood floor refinishing contractor prior to choosing maple flooring for your home.
Hickory Hardwood Flooring
Hickory is yet another popular flooring option, and for good reason. It is an extremely versatile type of flooring and can be used for more challenging flooring options homeowners want such as rustic wide plank farmhouse style interiors.
It is also one of the hardest, most durable hardwood flooring options out there as well. However, there are drawbacks to hickory. It is more prone to warping than other hardwoods. Additionally, hickory floor installation can be challenging as well.
You’ll definitely want to contact flooring experts in the Chicago area, such as Plus Hardwood Flooring if you’d like to get hickory hardwood floors installed in your home!
American Black Walnut Hardwood Flooring
American black walnut flooring has long been a staple in homes across the country. It has a beautiful appearance, with tight grains and striking undertones. This hardwood is also easy to stain as well, yet another advantage of this terrific flooring option.
However, American black walnut is often more expensive than other hardwood flooring options, It is also softer than many other wood species, so upkeep can be more challenging as well. Still, if you’re interested in looking at all your flooring options, make sure you talk about American black walnut to any of the professional flooring companies in Chicago to see if this classic hardwood is a good fit for your home or lifestyle.
Any of these hardwood flooring choices can be great options for your home, so talk to a trusted Chicago hardwood flooring company today to find out which one will work best for you!
3 Ways Hardwood Flooring Adds Value to Your Home
If you’re getting ready to put your home on the market, you should definitely consider installing hardwood floors, or refinishing the ones you have.
If you’re getting ready to put your home on the market, you should definitely consider installing hardwood floors, or refinishing the ones you have. And while hardwood floors are a thing of beauty, did you know they can help improve your bottom line, too? Here are three ways hardwood flooring adds value to your home.
1. People Want to Live in a Home with Hardwood Floors
If you’re planning on selling your home at some point in the future, you should definitely consider hardwood flooring. People looking for a new home consider many different factors in their search, and one of them is the type of floors a house has. In fact, according to a USA Today survey, about 25 percent of buyers under the age 54 prefer homes with hardwood floors in them. So, if you want your home to stand out when a realtor shows it to prospective buyers, you should definitely install hardwood flooring.
2. . . . . and They’ll Pay More for it
Another way hardwood floors add value to your home is buy increasing its resale value. Because so many prospective home buyers across nearly all age groups prefer hardwood floors, they’re willing to pay more for a home that already has them. Exactly how much more is difficult to pin down, but the USA Today survey cited above indicated that, on average, home buyers were willing to pay an extra $2080 for homes with hardwood floors.
3. Sell Your Home Faster
If you don’t want your home to languish on the market for weeks or even months, you should definitely consider installing hardwood flooring. Most modern home buyers don’t want to see dull tiles, off-color rugs, or laminate flooring when they’re considering a new home. So, swapping out an outdated carpet for hardwood floor can add instant appeal and get your home from a showing to an offer really quick.
Home buyers are searching for homes with hardwood flooring, so make sure you give the people what they want! A hardwood floor can increase the value of your home and help you sell it faster, too. So, if you’re ready to increase your home’s appeal, install hardwood flooring as soon as you can!
Chicago Neighborhoods, a Hardwood Flooring Perspective
When looking for hardwood flooring in Glenview, Illinois, you don’t have to ask around much before Plus Hardwood is mentioned…
In the greater Chicago area, there are countless suburbs and neighborhoods. Plus Hardwood Flooring focuses on hardwood floor installation in Chicago and beyond. Through our time working countless jobs in the area we’ve developed a love and appreciation for this city and its surrounding areas, not just for the beautiful neighborhoods and scenery, but for the people who call it home.
Our Base of Operations
When looking for hardwood flooring in Glenview, Illinois, you don’t have to ask around much before Plus Hardwood is mentioned. That’s because we are a Glenview-based hardwood floor refinishing contractor--Glenview is our home! We love Glenview for the space it provides away from the city, with nature preserves and botanical gardens accessible to clear the mind from the hustle and bustle of city streets. If you are in the Chicago area, Glenview is absolutely worth a visit.
Service to Chicago and Beyond
Though we will always have a special connection to Glenview, we offer hardwood floor refinishing and installation to the greater Chicago area, particularly the other North Suburbs. If you need hardwood flooring in Glencoe, for example, we fully capable of servicing you for no extra charge.
In addition, we provide hardwood flooring to Naperville residents, Lake Forest, Libertyville, Arlington Heights, Lake Bluff, and more areas for hardwood flooring like Northbrook. The rule of thumb is: If you call yourself a Chicagoan, we can come to you.
Conclusion:
Finding quality hardwood floor contractors to service or replace your Chicago hardwood flooring can be a challenge. Luckily, Plus Hardwood Flooring knows the area like the back of its hand, with trucks ready to deploy to you at your home as soon as we get your call. Whether looking for rubio monocoat installers, hardwood floor oil finishes, or hardwood floor refinishing contractors, Plus Hardwood has the answers to your questions--and a price to be happy about!
Rubio Monocoat: High-Tech Wax from the Future
In the world of hardwood floor contractors, Rubio Monocoat is a buzzword that is thrown around a lot these days. A Rubio Monocoat floor is comprised of a hardwood floor oil finish that has unique visual and durability properties. Created through applying a special blend of natural oils and waxes that bond to the wood from the inside, Rubio Monocoat floors form a watertight coating that is very durable. The color choices are incredible as well with 40+ inter-mixable colors; there are many mixes available to make virtually any look you can dream up possible.
What is Rubio Monocoat?
In the world of hardwood floor contractors, Rubio Monocoat is a buzzword that is thrown around a lot these days. A Rubio Monocoat floor is comprised of a hardwood floor oil finish that has unique visual and durability properties. Created through applying a special blend of natural oils and waxes that bond to the wood from the inside, Rubio Monocoat floors form a watertight coating that is very durable. The color choices are incredible as well with 40+ inter-mixable colors; there are many mixes available to make virtually any look you can dream up possible.
Is Rubio Monocoat right for me?
To determine if a Rubio Monocoat floor is the right type of hardwood floor oil finish for your home, a few things should be considered: desired visual style, budget, and durability needs.
Rubio Monocoat finishes have a unique Matte look and feel that is perfect for rustic, raw home aesthetics. For homes that want to have a more stylized and bright feel, Rubio Monocoat may take the backseat to traditional polishes and lacquers.
Though Rubio Monocoat may be slightly more expensive than other hardwood floor oil finishes, it lasts much longer than normal finishes (up to 10 years!) and is still cheaper than refinishing old hardwood floors.
Conclusion
Whether looking for Chicago hardwood floor contractors or around the globe, a rubio monocoat floor can make a huge difference in your home’s overall appearance. With a stylized matte feel, competitive price, and fantastic durability, it’s a no-brainer to at least consider rubio monocoat when selecting a hardwood floor oil finish.
For all your hardwood floor contractor needs, feel free to reach out to us at Plus Hardwood Flooring for a complimentary Rubio Monocoat estimate and consultation.
Refinishing vs Replacing Hardwood Flooring
Hardwood flooring, while durable, still wears from years of heavy use. There comes a time when every homeowner with hardwood must make an important decision: to refinish or replace their hardwood floors. Keep reading to discover the pros and cons to each, and what to look out for when choosing hardwood floor refinishing contractors.
Should you refinish or replace hardwood floors? That’s a question so many homeowners ask themselves. Hardwood flooring, while durable, still wears from years of heavy use. There comes a time when every homeowner with hardwood must make an important decision: refinish or replace.
Keep reading to discover the pros and cons to each, and what to look out for when choosing hardwood floor refinishing contractors.
Pros and cons of Refinishing
Hardwood floor refinishing is without a doubt the most cost-effective option for keeping hardwood floors looking brand new. Hardwood floors can be refinished up to ten times, meaning once you invest in an artisan hardwood floor, that investment can last a lifetime. This is a compelling argument for going the refinishing route, as adding a new hardwood floor oil finish like rubio monocoat can completely invigorate the look and feel of your flooring.
However, refinishing has its cons, such as not being a completely new floor. At times, a homeowner may want to choose a totally different grain or type of wood, in which case refinishing would not be a great option. 99% of the time, however, your local hardwood floor refinishing contractors will have the color and finish desired to revamp your flooring’s feel.
Pros and cons of Replacing
Whether looking for Chicago hardwood flooring or across the nation, any hardwood floor contractor will tell you that nothing is quite like brand new hardwood. Going the replacement route ensures a sparkling new floor that can have unique grains and patterns not offered through refinishing. Since the actual wood is being replaced, any rot or decay that is permanent damage is mitigated--something that could be an issue with refinishing alone.
Ultimately, the health of the floor (whether or not there is excessive damage), and the homeowner’s budget are the two biggest considerations for going the replacement route. If the floor is truly damaged beyond repair, replacement is the best option.
Conclusion
So should you refinish or replace hardwood floors? While situations may arise that make replacing hardwood floors the best option, the majority of floors that are in rough shape simply need a professional hardwood floor refinishing job to have that ‘brand-new’ look and feel. When looking for floor refinishing in Chicago, Plus Hardwood Flooring has earned its stripes with dozens of successful jobs, particularly with rubio monocoat floors that last for decades.
Hardwood Floor Refinishing Tips: What Machines to Use
Trying to figure out what tools you’ll need for sanding and hardwood floor refinishing? Well look no further! Read this article to find out about refinishing tools.
Looking for hardwood floor refinishing tips? If you’re trying to figure out what tools you’ll need for sanding and refinishing, look no further! Below is a comprehensive list of what tools you’ll need, what each tool is for, and tips on how to use each tool.
The Drum Sander
This machine does a lot of the work in the sanding and refinishing process. When it comes to refinishing old hardwood floors it removes old stain or finish and levels any excess wood. The drum sander is comprised of a drum made of metal that is sleeved with rubber to cushion contact with the floor. Then there is sandpaper wrapped around the rotating drum that removes small amounts of uneven wood, old stain, and old finish.
There are four ways that drum sanders are specified: drum size, voltage, drum-elevating method, and sandpaper type. The most common size and best option for DIYers that are trying to do some hardwood floor refinishing for the first time would be 8-inch sanders with 110 voltage. These types of sanders are easy to maneuver which means that you are less likely to make a mistake or any harsh errors.
If it’s your first time using a sander there are some precautions, you should take as far as safety. Make sure you always unplug the sander when adjusting anything with the machine and heavier sanders are equipped with belts, which will help take the burden off your arms and give the machine a smoother cut.
The Edger
When it comes to areas that the drum sander can’t reach, that’s where the edger comes in handy. The edger’s rotating disc can get close to walls and help perfect the hardwood floor refinishing job. They are ideal to use in tight areas such as closets.
The edger is a large motor connected to a shrouded disc that ranges from 5 to 7 inches. Each wheel is adjustable, helping you perfect the depth and angle of the cut. Even though the edger is small it removes more wood per square foot than any other floor machine. Therefore, if you aren’t careful you can easily mess up and leave bad gashes.
The Buffer
If you’re looking to complete a high-quality hardwood floor refinishing job, then you need to use a buffer. The buffer is used for a final, fine abrading of the wood floor before newly staining and finishing the floors. This helps blend all areas of the floors together and make it look seamless.
Buffers are fitted with a screenback, which is a fine abrasive disc. The screens come in various diameters, from 60 grits to 180 grits. When you screen between coats of finish it’ll take a bit off the top making for a smoother final finish.
We hope you enjoyed these hardwood floor refinishing tips. Now you know all there is to know about the machines that will help you refinish old hardwood floors and make them look new again.
And as always, if you'd like to schedule a hardwood flooring project with us, feel free to contact us via our contact page. We look forward to working with you!
And don't forget to follow and like us on Facebook at www.facebook.com/plushardwoodflooring to make sure to always get the latest updates!
Plus Hardwood Flooring 2018 Highlights
It’s January! Time to reflect on 2018, specifically the work of one of your favorite flooring companies in Chicago. Plus Hardwood Flooring has done some amazing projects this past year, ranging from installation to sanding and finishing.
It’s January! Time to reflect on 2018, specifically the work of one of your favorite flooring companies in Chicago. Plus Hardwood Flooring has done some amazing projects this past year, ranging from installation to sanding and finishing. So, let’s take a deeper look at some highlight projects from this year and why they stand out amongst the rest.
Rubio Monocoat Floor for a Large Local Builder
This project focuses around a beautiful entryway. The floors, a wide plank white oak, were installed by another company, but the customer, a local builder, chose to reach out to us to sand and finish his floors. This was a unique scenario because the local builder had regular flooring companies he worked with, but wanted to work with us due to the fact that our sanding and finishing techniques are one of the best out of all the flooring companies in Chicago. The entryway floors were finished with Rubio Monocoat Hardwax Oil in smoke 5%. This Rubio Monocoat floor had a herringbone layout making the entryway look grand and beautiful.
Chevron Patterned Brazilian Cherry Hardwood Floor
This was a very special project because of its size, 4,500 square feet, one of our biggest jobs in 2018. For this job we were actually recommended by a different flooring company in Chicago. The scale of the job and expected quality lead to the recommendation. He knew his friend needed to work with one of the best flooring companies in Chicago! For this project we refinished Brazilian Cherry floors with minor patchwork and board replacements. After that everything was sanded down with our special Dustless Lagler Trio Sanding Process and refinished to a natural, clear finish using water-based products.
A Little Rubio Monocoat Floor Adventure
This project was smaller than the other two, but that doesn’t mean it was any less interesting! It actually stands out because of its fun process and the color involved. This Rubio Monocoat Hardwax Oil project involved “fuming”, so after we finished the floors, we had to fume them in order to get a natural grey base color out of the wood. This process is one of the hardest and is normally only done on new floors. Why new floors you might ask. Well, many issues can arise on old floors with really deep sanding. When this is the case you need to make sure to fume the floor really well. After the “fuming” process we put Rubio Monocoat Super White color oil on top for an awesome two-tone effect. The challenge on this Rubio Monocoat floor ended up great, and we are happy we rose up to the occasion!
Well that is a wrap up of 2018 from one of your favorite flooring companies in Chicago! And as always, if you'd like to schedule a hardwood flooring project with us, feel free to contact us via our contact page. We look forward to working with you!
And don't forget to follow and like us on Facebook at www.facebook.com/plushardwoodflooring to make sure to always get the latest updates!
Prefinished vs. Unfinished Hardwood Flooring
Wondering if you should install prefinished hardwood for the ease? Or pick unfinished hardwood for the beauty? You should love the floors you put in your home, so learn more about your flooring options.
Wondering if you should install prefinished hardwood for the ease? Or pick unfinished hardwood for the beauty? When it comes to prefinished vs unfinished hardwood flooring, the main difference is that prefinished hardwood flooring has been sanded, stained, and coated in a factory. Therefore, all that is left is installation. While unfinished flooring is raw hardwood that will get installed first then sanded and refinished in your home.
Overall, the floor you choose in your home is something that will be there for a while, so you have to love it, know all your options, and choose which option will be best for you. Below we have included multiple pros and cons for prefinished and unfinished hardwood flooring, to help you with your decision-making process.
Prefinished Hardwood
One big advantage of prefinished hardwood is time! It’s a one-step process, once the installation is done, the floors are fine to walk on and put furniture on. There is also less mess with prefinished flooring. Since you are skipping the sanding process, that cuts down on dust and dirt.
Also, prefinished hardwood will cost less overall. The initial cost will be more, but there normally is also a reduced labor cost that makes it a cheaper process. The downside of prefinished hardwood is that you can’t always customize it the way you want.
Unfinished Hardwood
A big advantage of unfinished hardwood is the stunning look it has. It looks like real wood, unlike most prefinished hardwood, even though both are often real. Since unfinished hardwood is finished in your home by a professional, instead of a factory, it really looks like a work of art!
There are also more creative possibilities with unfinished hardwood because you can choose the finish options. A downside is the time it takes to install, sand, and finished unfinished hardwood flooring. But, for floors you’ll love, they will be worth the wait.
And as always, if you'd like to schedule a hardwood flooring project with us, feel free to contact us via our contact page. We look forward to working with you!
And don't forget to follow and like us on Facebook at www.facebook.com/plushardwoodflooring to make sure to always get the latest updates!
Pros and Cons of Choosing Hardwood for the Stairs
Want to learn more about having a hardwood staircase? We’ve laid out the pros and cons, giving you advice on your flooring options.
Not sure if a hardwood staircase is a must in your home? There are many great reasons why hardwood flooring is the best choice, yet it’s important to fully know what you are getting into, as far as safety and appearance. Below we have laid out the pros and cons of getting a hardwood flooring staircase.
Pros
Hardwood flooring on the staircase won’t accumulate as much dust and dirt as other flooring options such as carpet, therefore cleaning will be super easy and manageable. Stains won’t be a concern either because if you spill something on hardwood it’ll be an easy clean up. Another good thing about hardwood is that if the area around the staircase is mostly hardwood flooring, the flow and appearance of your home will look more seamless. Hardwood compared to other materials is also very versatile. It can have a modern and new age feel but also a classic touch to it, making it perfect for any theme throughout your home.
Cons
One thing you might have to worry about when it comes to hardwood flooring on the stairs is the safety factor. Hardwood staircases can be slippery and dangerous for small children or elderly. Yet, a hand railing or no-slip stair treads can solve that problem for you if you decide hardwood is a must on your staircase. Another thing is that hardwood is often pricier than other materials, but it will increase the value of your home.
Overall, hardwood flooring is a great choice, and if you have any other questions feel free to contact us via our contact page. We look forward to hearing from you!
And don't forget to follow and like us on Facebook at www.facebook.com/plushardwoodflooring to make sure to always get the latest updates!
Hardwood Flooring Outside: The Best Wood For Outdoor Living
Even though we are in the winter months it’s never too early to start brainstorming for spring and summer renovations. Know which types of woods are great for your patio or deck.
Even though we are in the winter months it’s never too early to start brainstorming for spring and summer renovations. Installing hardwood floors in outdoor living spaces, like a patio or a deck, can get complicated especially when outside weather conditions are unpredictable. You might be thinking, if the maintenance of hardwood can be complicated when in an outdoor living space, why not just use a different material? Well, stone and tile can get expensive, and cement can be difficult to repair if it cracks. Therefore, installing hardwood floor with the correct planning process can be the best option.
Now here are the most popular wood species to consider for outdoor living spaces!
Redwood
This is usually the number one choice for outside wood flooring. Not only is it beautiful but its ability to resist shrinking, warping, and cracking make this one of the best choices. It also is resistant to decay and insects. Redwood retains finishes well and is very maintenance free, so you won’t be worrying about it in the rain or snow.
Tigerwood
This is an incredibly beautiful wood species and is used for multiple uses because it accepts stains really well. This species comes in colors from very dark red to a reddish brown. It’s extremely strong and is also resistant to insects and termites.
Mahogany
Mahogany ranges from tan to auburn brown. This is also a very strong and dense wood species. Normally, this is the best porch flooring material for houses located along the coast, in rainy, or humid communities.
Cedar
This wood species is known for its beauty and durability. Cedar normally ranges from mellow ambers to reddish browns. It is resistant to decay and insects due to the oils in the wood making it great for the outside.
And as always, if you'd like to schedule a hardwood flooring project with us, feel free to contact us via our contact page. We look forward to working with you!
And don't forget to follow and like us on Facebook at www.facebook.com/plushardwoodflooring to make sure to always get the latest updates!
Tips for Protecting Your Hardwood Floors During the Holidays
Your home is about to get a lot of traffic with holiday season right around the corner. Make sure you are prepared to protect your hardwood floors.
Wondering how to protect your hardwood floors during the holidays? Your home will get a lot of traffic during the holiday season, and it’s important to keep up with cleaning and maintenance on your floors so when it’s all said and done in January you don’t panic that your hardwood is completely ruined. Below is a list of things to keep in mind while having guests over, even if it’s a small crowd.
Don’t Automatically Pull Out the Mop
When there is a spill, I know it is tempting to just take out the mop and wipe the whole area of the floor down. It’s quick, it’s easy, but it will also dull the finish and be harmful for your floors. It’s better to take the time and clean it up with dry products or use a hardwood floor cleaner that won’t damage your floors.
Buy a Tray for Your Tree
Real trees are beautiful and fragrant, but they also can ruin your hardwood floors. It’s important to have something under your tree to protect your hardwood from dirt, scratching, and water damage. Being precautious is better than not putting anything under the tree, because once that tree is up it’s up for a good chunk of time.
Felt Pads Under all Decorations
Putting up decorations is fun! You get to blast holiday music and decorate your home. Yet, wood tables and floors can get a beating when moving and shifting things. Make sure to put felt pads under all decorations so that you can move them however you want without any headache.
Clean Before Don’t Just Wait till After
It might make sense to wait until after a big party to clean, but it’ll be easier to clean before and after the party. This way the mess becomes manageable after the party, and you end up having to clean less than you thought you would. It also ensures that your floors are always in tip top shape.
And as always, if you'd like to schedule a hardwood flooring project with us, feel free to contact us via our contact page. We look forward to working with you!
And don't forget to follow and like us on Facebook at www.facebook.com/plushardwoodflooring to make sure to always get the latest updates!